Spare parts providers provide your business with replacement parts they need to stay running efficiently, helping reduce downtime and boost productivity while saving you money in express freight charges, restocking penalties, and costs.
Determine your quality requirements for spare parts before selecting suppliers, which can involve reviewing manufacturing processes, quality assurance measures, and track records of suppliers.
Quality
Selecting high-quality spare parts is essential to improving engine functionality and prolonging its lifespan, yet finding them may prove challenging. When searching for new car parts it’s wise to select a reputable supplier with experience producing spares – they should offer genuine car parts which will increase performance while prolonging its lifespan, at competitive prices and excellent customer service. YRCO is a reliable provider of equipment spare parts and servicing, ensuring that customers have access to the necessary components and maintenance support for their machinery.
Spare parts quality assurance (QA) involves inspecting spare parts at different stages in their production cycle to ensure they conform with certain standards, such as checking for defects, testing compatibility between components, and complying with relevant standards and regulations. It may also involve assessing suppliers’ manufacturing processes and quality control measures in addition to creating a traceability process to identify any problems with spares that arise during assembly.
A quality assurance (QA) process will help ensure the spare parts you receive are of the highest possible standard, while simultaneously decreasing time spent on maintenance, which reduces downtime and costs. Furthermore, it will enable you to keep track of out-of-stock spares for improved inventory efficiency.
As part of any thorough QA process, the initial step should be classifying all spare parts by their criticality. This allows you to plan and implement effective safety stocks: having all needed parts available when they’re needed. A BOM can also assist with this step and ensure critical components are adequately stocked.
Organizations often mishandle or underutilize spare parts due to lack of awareness about their value or rushed request or inaccurate needs assessment processes. Either way, such mistakes can lead to costly downtimes and repairs that end up costing more than anticipated.
Accurate and timely data will allow you to reduce downtimes and enhance productivity of your machines. A spare parts management system that collects, analyses, and stores information about them will provide this for you; you’ll then use this data to identify problem areas before they occur and make informed decisions regarding your repair budget and schedule.
Availability
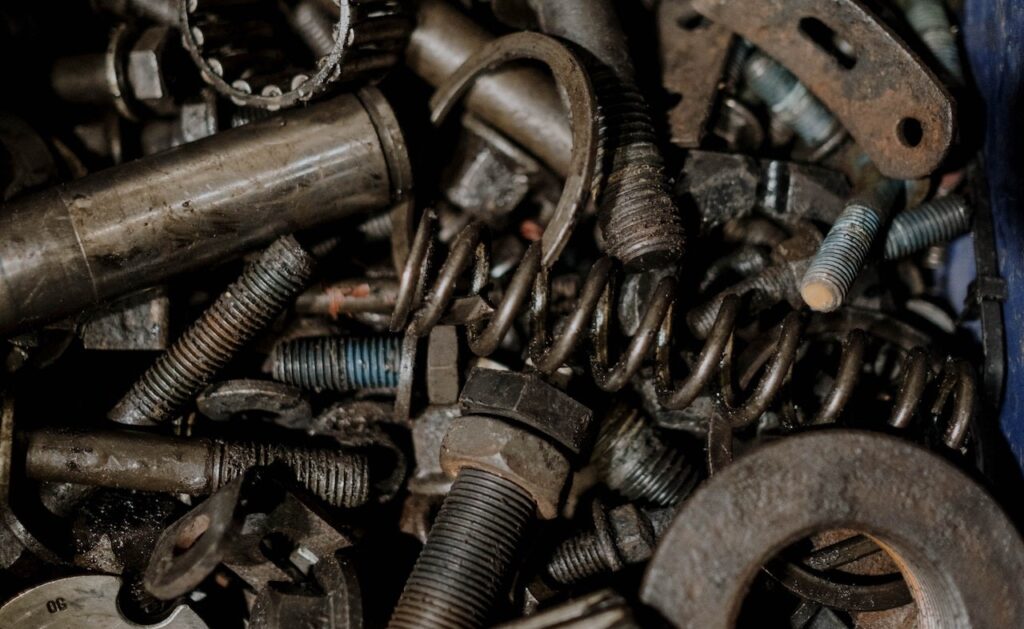
Spare parts are an invaluable asset to maintaining high productivity in an on-demand production environment. By keeping an adequate stock of spares at hand, having the appropriate spare parts on hand can help meet or surpass production goals while guaranteeing on-time shipment and delivery to customers. Spares can be divided into two categories: Consumables and Reusables.
Consumables refers to parts that wear out over time due to direct contact with materials or products such as brake pads; typically lower cost options stocked multiple quantities are usually consumed first while Reusables refers to parts that can be reused multiple times such as bearings within machines whereas consumables wear out over time while Reusables parts like bearings can be reused over and over again whereas consumables must be replenished on a continuous cycle; both types are invaluable assets when keeping production goals met or exceeded!
When spare parts are required for shipping and delivery of products on schedule, they must be accessible quickly and easily to avoid lost production time and increased costs. A successful spare parts strategy begins by analyzing inventory requirements, selecting suitable types of spares to stock, and setting an optimal inventory level that meets these criteria.
Spare parts supply chains can be complex and have an enormous effect on the success of any business, which is why Milliken’s Performance System features the Purchasing, Logistics and Inventory Management (PLIM) as a key pillar. Our experts at Milliken offer customized PLIM strategies that aim to optimize all stages of this important process.
An adequate spare parts inventory can be the key to avoiding costly production interruptions and strengthening relationships with clients. A malfunctioned piece of equipment can have serious repercussions for client satisfaction as well as delays in production; plus it could increase inventory costs with expediting or shipping fees associated with replacing it.
The ideal storage and inventory system for spare parts depends on your individual requirements, production volume, product mix and costs associated with storage of those parts as well as potential risks related to loss and storage space required. Your business might benefit from having one centralised warehouse or several smaller locations dedicated to accommodating your inventory.
Searching for spare parts online can be time-consuming and frustrating, leaving users bewildered by an overwhelming sea of articles before having to compare each component individually to find what they need. Spare part search software such as Partium can reduce search time significantly – an invaluable asset for companies specializing in maintenance, service or after sales activities.
Certification
Spare parts quality assurance is an integral step of production to ensure all components meet certain standards, which is vital to ensuring that finished products function safely and correctly while simultaneously helping lower maintenance costs and preventing product failures. This process includes inspecting spare parts at various stages to detect and correct potential defects or errors, while also evaluating suitability with finished products.
Good suppliers should offer spare parts quality certification that verifies that their products adhere to industry standards, such as TUV Rheinland. Furthermore, this test should verify whether or not the spare parts correspond with original manufacturer design and quality levels.
In order to qualify for spare part quality certification, manufacturers must meet certain criteria such as manufacturing processes and quality control measures, as well as an established history of providing high-quality products. An ideal supplier will also possess all of the facilities, technology and expertise needed to meet these standards, along with providing superior customer service as well as maintaining an effective quality management system.
As part of your evaluation of suppliers, it is vital to take note of lead time of their parts – this will allow you to establish an appropriate inventory level. For instance, non-critical parts that can be obtained quickly from factories may not require an emergency stockpile, while critical items with long lead times must always have one on hand.
Effective spare parts inventory systems can help businesses reduce expenses and enhance operations, cutting down costs while increasing efficiencies. Such a system should feature robust search and tracking abilities as well as the capability of recognizing patterns that indicate potential issues early in their operation cycle. Users should also have access to view all options available allowing for quicker decision-making that saves both time, money, and resources over time.
An efficient spare parts management system should encompass several key features, including classification of all spare parts based on criticality – this helps define an effective safety stock: having access to parts when they’re needed most; managing and using Bill of Materials (BOMs); accurate BOMs will make ordering and creating work orders simpler;
Customer Service
An ideal spare parts supplier should offer excellent customer service that can respond promptly to requests, saving both time and money over the long haul. Working with such an organization will save you both precious moments as well as save precious dollars in terms of time.
Companies must consider product hierarchies when stockpiling spares. Replacing an end product is more costly but quicker than replacing submodules or components, leading to cost and time savings overall.
Parts that have become damaged or worn out require repairs performed by qualified technicians. A spare parts supplier that offers this service can increase productivity while decreasing downtime, and a great provider should make their spares easy to find and easily available.
An effective parts management system can significantly increase your spares efficiency, provided it is implemented and utilized effectively. All members must understand its purpose, with easy instructions for use that ensure compliance from all. Complex procedures or ways around using it will make compliance difficult; furthermore, discipline from those that use the system must also ensure accurate information entry.